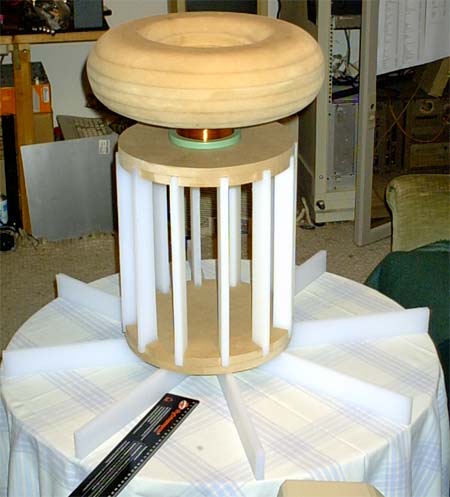 |
This picture shows the first parts I made to construct an new driver unit for my next magnifying transmitter. To achieve the desired coupling the secondary is 12" in diameter and 12" high. The primary will be made of 2" wide copper strap and will consist of 6 or 7 turns. This way I can adjust the coupling up to 0,45, that should be sufficient I hope.
The white pieces are made from 1/2" LDPE kitchen board. I intend to wind this coil with 100 turns of AWG16 stranded wire.
The table is unfortunately not mine, but it would fit perfectly to carry the components ( without the tabelcloth of course ;-)
|
You probably already wondered what that strange looking toroid is made of...it's made from MDF, several layers glued together and then ground into shape. This is probably the most work intensive, silliest way to make a toroid but I hade some spare time...OK, that's not really a good excuse... ;-)
The result wights in at about 6KG and when coated with aluminium tape will be nearly undestroyable. The spool of magnet wire is just sitting there to support the toroid for the photo.
|
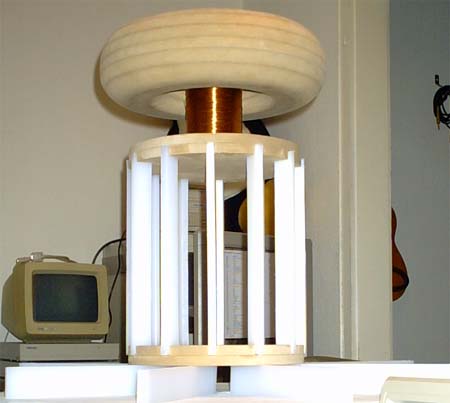 |
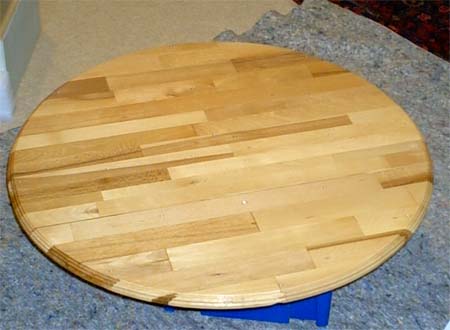 |
This is the base made from beech laminated wood. The edges are shaped by means of a router. |
Here you can see the base with the primary supports and secondary coil. |
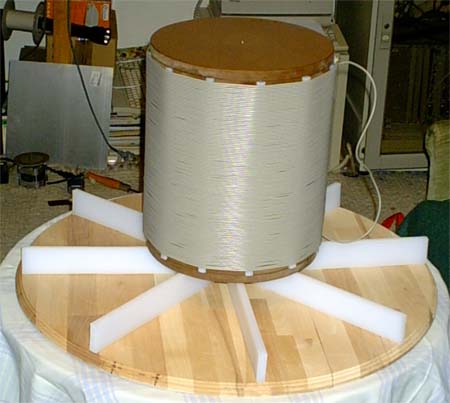 |
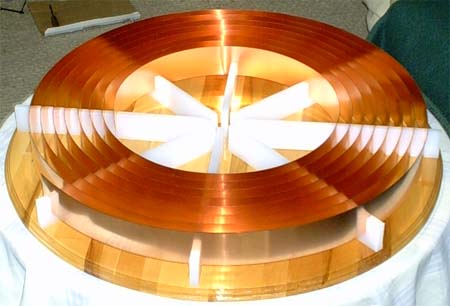 |
Here you can see the base with the finished primary coil. The copper ribbon is 6cm wide and offers nearly eight turns for tapping.
The wooden base was polyurethane varnished several times. |
Here you can see the finished primary with the secondary coil in place. |
 |
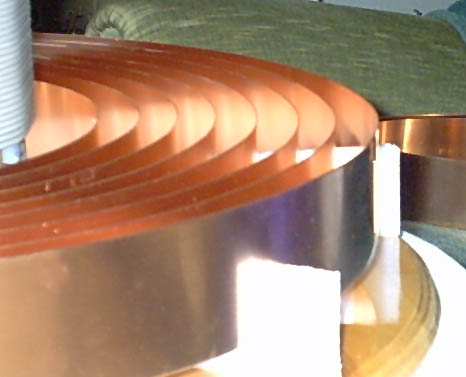 |
Closeup view of the outer turn, showing how the copper ribbon fits into the suports and the finish of the wooden base.
|
The toroid with the aluminium tape applied. This did not work out as smooth as I had hoped, but it
is not as uneven as the picture makes it look.
Maybe I will rework this part some other time. |
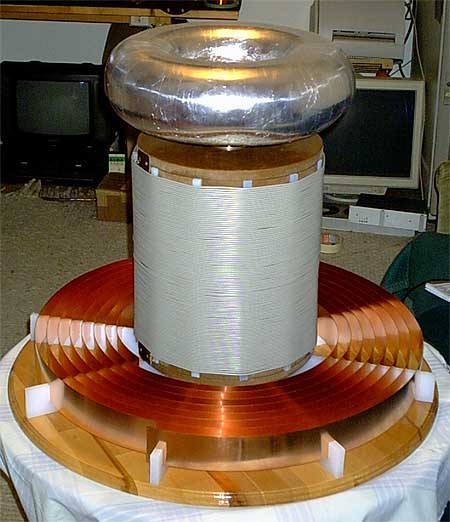 |
Varnishing job finished. All parts are polyurethane varnished for
a nice finish and good insulating properties. The insulator on the lower left
will be the connection point for the primary tap connection.
|
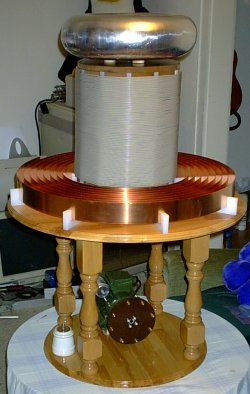 |
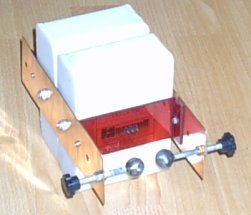 |
The cap bank including the two maxwell pulse caps,
safety gap and two microswitches to monitor any bulging of the cases.
The microswitches will serve as emergency shutdown in the case of cap failure.
|
The cap bank with the insulating posts in place.
The connecting metal disks are those metal washers you use in bench grinders to
hold the disks on the shaft. You can certainly imagine what happened to the
grinder and that it has no need for these disks anymore ;-)
|
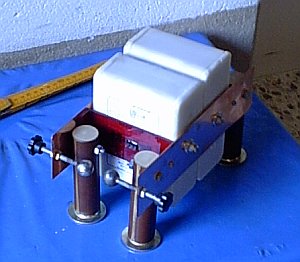 |